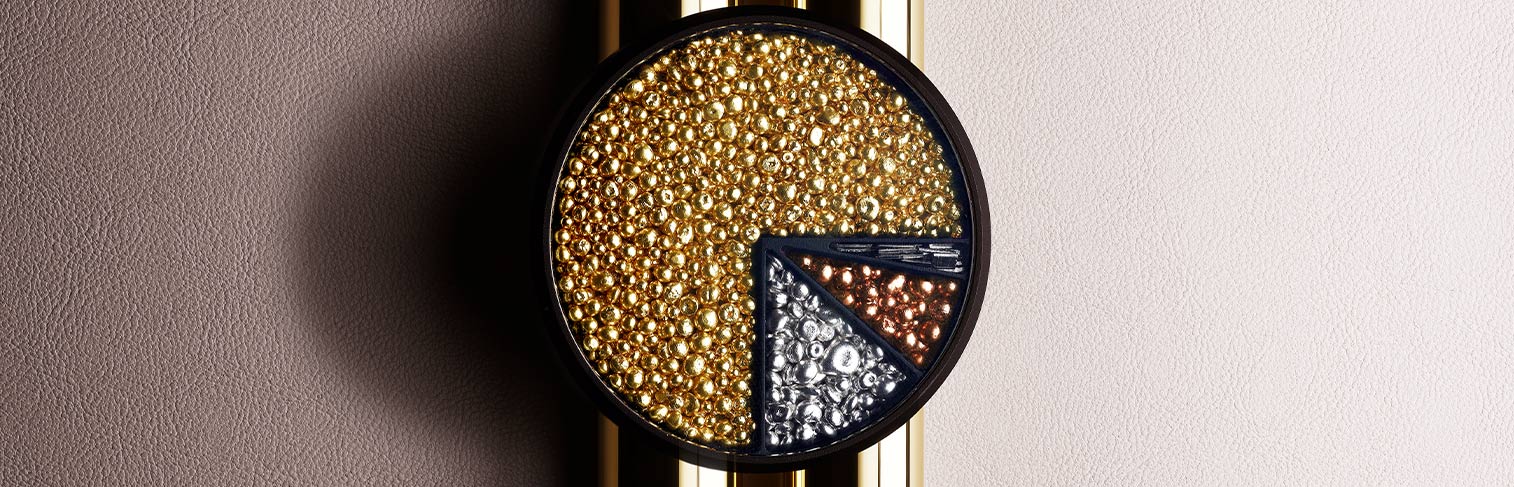
Uhrengehäuse - Schutz und Ästhetik am Handgelenk
von Gisbert Brunner am 13.06.2022
Im Gegensatz zum Uhrwerk, präsentiert sich das Gehäuse einer Armbanduhr ausgesprochen öffentlichkeitswirksam. Gemeinsam mit Armband, Zifferblatt und Zeigern prägt es den ersten und sicherlich auch bedeutendsten Eindruck. Unter anderem sorgt das illustre Ensemble für den bei Luxus-Zeitmessern immens wichtigen Wiedererkennungswert. Über Schönheit lässt sich in diesem Zusammenhang selbstverständlich streiten, denn hier spielt der eigene, individuelle Geschmack und Stil die entscheidende Rolle. Worüber sich jedoch nicht streiten lässt: Das Gehäuse ist Schutz fürs Uhrwerk, muss eine gewisse Funktionalität und den nötigen Tragekomfort aufweisen. Das wird jeder Uhrenliebhaber bestätigen.
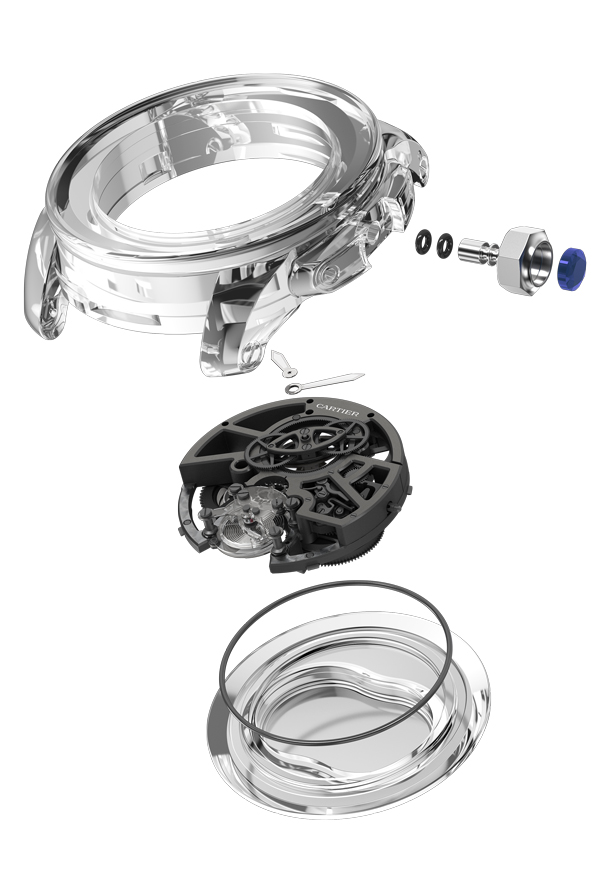
Herstellung des Uhrengehäuses
Am Anfang jedes Gehäuses steht eine Idee, ein kreativer Prozess, der sich in Skizzen ausdrückt. Stößt das Gezeichnete auf Anerkennung, geht es an die technische Umsetzung durch Computer. Mit dieser Hilfe entstehen dreidimensionale Grafiken und inzwischen auch Drucke, die realitätsnahe Eindrücke vermitteln.
Danach sind die Prototypisten bei den Gehäusefabrikanten gefragt. In reiner Handarbeit produzieren sie erste Exemplare aus leicht zu bearbeitendem Material. Trageversuche geben Aufschluss über Ergonomie, Komfort und den Auftritt am Handgelenk. Tests zeigen, ob Belastbarkeit und Wasserdichtigkeit den Vorgaben entsprechen.
Modifikationen und Regeln sind in diesem Geburtsstadium an der Tagesordnung. Erst wenn tatsächlich alles passt und die in Pflichtenheft verewigten Kriterien ausnahmslos erfüllt sind, erfolgt die Freigabe zur Serienfertigung.
Eine Gehäusefabrik verlangt nach einem breiten Spektrum unterschiedlicher Berufe und Kompetenzen: Designer, Konstrukteure, Prototypisten, Werkzeugmacher, Stanzer, Maschineneinrichter und -beschicker, Polisseure, Monteure, Goldschmiede, Steinsetzer und dazwischen immer wieder Kontrolleure.
Am Anfang jedes Metallgehäuses steht ein Rohling. Nur große Serien rechtfertigen die kostenintensive Herstellung von Stanzwerkzeugen. Je nach Aufwand kostet ein einziges mehr als 10.000 Euro. Komplexe Gehäuse verlangen bis zu zwanzig dieser Geräte. Mit Drücken von 30 bis 120 Tonnen werden Metallstücke gnadenlos in die gewünschte Form gepresst. Danach erledigen computergesteuerte Fertigungszentren das Fräsen und Bohren mit einer ganzen Batterie unterschiedlicher Werkzeuge auf den Hundertstelmillimeter genau. Alternativ zu diesem geteilten Verfahren bringen Maschinen aber auch komplette Gehäuse zustande.
Währenddessen befassen sich andere Maschinen mit der Produktion des Bodens und - sofern vorhanden - des Glasrands. Die erforderlichen Koordinaten kommen auf digitalem Wege von den Konstruktionsbüros. Durch die ständige Bewegung und Erwärmung der Maschinen regelmäßige Stichprobenkontrollen an der Tagesordnung. Dadurch soll der Verschleiß klein gehalten werden. Stimmen die Ist- nicht mit den Soll-Daten überein, heißt es Handeln. Gegenüber dem ursprünglichen Rohling hat das fertige Produkt rund zwei Drittel seines Gewichts verloren. Dass kostbare Edelmetall-Abfälle penibel gesammelt, gewogen und wieder eingeschmolzen werden, mag sich in diesem Zusammenhang von selbst verstehen.
Vor der Politur werden noch die verschiedenen Gravuren angebracht. Entweder traditionell mit Pantographen oder auf moderne Weise per Laserstrahl. Apropos Politur: Zur traditionellen Handarbeit gesellen sich mehr und mehr Roboter. Die arbeiten zwar nicht schneller, dafür aber unermüdlich. Anschließend sind die Monteure am Zug. Sie fügen die diversen Komponenten, darunter auch zugekaufte wie Saphirglas, Dichtungen, Aufzugskrone und gegebenenfalls Drücker zu jenem Ganzen zusammen. Vor dem Verlassen der Fabrikationsstätte erfolgen die Prüfung der intendierten Wasserdichte und eine penible Endkontrolle. Selbst minimal Fehlerhaftes geht zurück, denn der Kunde ist König.
In folgender Bilderreihe sehen Sie den Prozess von der Gehäusefertigung über die Schleiferei bis zur Gehäusezurichtung.
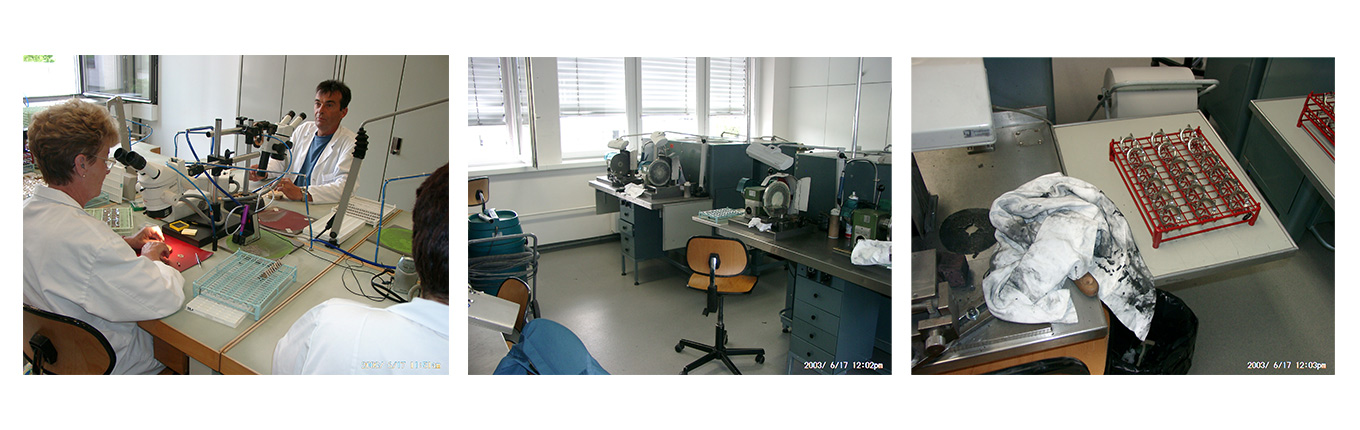
Materialien eines Uhrengehäuses
Gold
Traditionsgemäß bestehen die Gehäuse tragbarer Uhren aus Metall. Besondere Faszination übt dabei Gold aus. Etwa 30 Milliarden Tonnen der „erstarrten Lichts der Sonne“ birgt die gesamte, gerade einmal 15 Kilometer „dünne“ Erdkruste. 1.000 Kilogramm beinhalten drei bis fünf Milligramm. Für eine effiziente, kostendeckende Gewinnung ist das allerdings viel zu wenig.
Der physikalische Steckbrief von Gold ist seit vielen Generationen bestens bekannt: Ordnungszahl 79 im periodischen System, Atomgewicht 197, Dichte von 19,32 Gramm pro Kubikzentimeter, Schmelzpunkt 1.063 Grad Celsius.
Herausragend sind die Korrosionsfestigkeit sowie die weitgehende Beständigkeit gegen Säuren und Sauerstoff. Wegen seiner Weichheit kommt 24-karätiges Feingold für Uhrengehäuse nicht in Betracht. Aber zum Glück lässt sich Gold mit anderen Metallen legieren. Das führt zu größerer Härte und gestattet die Kreation ganz unterschiedlicher Farbtöne, unterteilt in Kategorien bis hin zu 5N.
- 1N präsentiert sich blassgelb mit einer Härte von 200 – 240 HV.
- 2N mit 175-220 HV tritt hellgelb in Erscheinung.
- 3N, das typische Barren- oder Gelbgold weist eine Härte zwischen 160 und 200 HV auf.
Roségold 4N und Rotgold 5N entstehen durch eine höhere Beimischung von Kupfer. 18-karätiges Roségold 4N besteht zu 75 % aus Gold, hinzu kommen 16 % Kupfer und 9 % Silber. Beim Farbton 5N steigt der Kupferanteil auf 20,5 Prozent bei nur noch 4,5 Prozent Silber.
Rolex ist mit „Everrose“, einer eigenen Rotgold-Legierung am Markt vertreten. Die lange anhaltende Farbstabilität resultiert aus einen höherem Kupferanteil und dazu noch einem „Schuss“ Platin.
- 4N-Gold besitzt übrigens eine Härte von 270 Vickers (HV).
- Bei 5N steigt der Wert auf 300.
Im Vergleich dazu bringt es Diamant, der „Unbezwingbare“ auf 10.600. Keramik liegt bei 1.500, Titan bei 970 und Stahl bei rund 700 HV.
Der Oberbegriff Weißgold trifft auf Legierungen zu, denen mit Silber, Platinmetallen oder anderen metallischen Zugabe die Farbe entzogen wurde. Je nach Zusammensetzung ergibt sich hellweißes (silbernes) bis grauweißes Gold. Bereits in den 1920-er Jahren setzte die Entwicklung erster Weißgoldlegierungen ein. Und zwar als Alternative zu Platin und Palladium. Letzteres hat trotz bestechender Eigenschaften so gut wie keine Verbreitung in der Gehäusefertigung gefunden.
Bei echtem Weißgold handelt es sich um einen homogenen Werkstoff. Will heißen: Er präsentiert sich durch und durch weiß. Manche Fabrikanten erzeugen diesen Farbton allein durch galvanisches Rhodinieren der Oberfläche. Solcherart kaschiertes Gelbgold darf sich nicht Weißgold nennen, obwohl der Begriff keiner Normierung unterliegt. Insofern kennt die Branche nahezu unzählige Weißgoldrezepturen mit unterschiedlichen Goldanteilen.
Die Tatsache, dass Goldgehäuse leicht verkratzen, rief die Industrie auf den Plan.
A. Lange & Söhne bietet „honiggoldene“ Referenzen an. Der Name resultiert aus einem sehr speziellen Farbton. Als Basis für diese Sonder-Legierung dient 18-karätiges Weißgold ohne Beimischung von Palladium, Nickel oder Silber. Für den dezent honigfarbenen Schimmer wird etwas Kupfer, Zink und Silizium beigemischt. Darüber hinaus bewirkt ein abgestimmtes thermisches Verfahren die beachtliche Härte von 320 HV.
Auf 1.000 Vickers Härte bringt es „Magic Gold“, eine Spezialität von Hublot. Mit der Entwicklung des gegen Kratzer weitestgehend unempfindlichen Werkstoffs, der sich trotzdem mit Fug und Recht Gold nennen darf, hatte die Manufaktur unter dem Dach des LVMH-Konzerns einen Lehrstuhl der Technischen Hochschule Lausanne beauftragt. 2011 debütierte das „Magische Gold“. Beim selbstverständlich patentierten High-Tech-Verfahren wird, ganz einfach gesagt, flüssiges 24-karätiges Gold mit rund 200 bar Druck in eine ultraharte, aber poröse Keramikstruktur gepresst. Die jeweiligen Quantitäten sind so genau berechnet, dass die fertigen Komponenten eine 18-Karat-Punze bekommen. Alles andere als ein Kinderspiel ist die Bearbeitung der Komponenten mit Diamant-Werkzeugen und Ultraschall. Mangels zufriedenstellender Resultate findet sich in den Werkstätten von Hublot inzwischen ein wassergeführter Laserstrahl, der seinen Job in der gewünschten Perfektion erledigt.
Mit „Fairmined“ verknüpft Chopard seine Bemühungen um nachhaltigen Luxus. Menschen mit Goldfaible können sich die Lebensbedingungen der Werktätigen am Anfang der Wertschöpfungskette kaum vorstellen. Deshalb startete das Familienunternehmen 2013 gemeinsam mit Partnern ein engagiertes, auf mehrere Jahre angelegtes Projekt. Zuerst profitierte die „Coodmilla Cooperative“ im kolumbianischen La Llanada von der Zusammenarbeit. In diesem Bergbaugebiet leben gut 1.800 Menschen von der Goldmine. 2015 wurde Coodmilla nach den Richtlinien fairer Goldgewinnung zertifiziert. Darüber hinaus unterstützt Chopard sein jenem Jahr zusammen mit der ARM die „15 de Agosto“-Cooperative, eine mehr als 4.000 Meter über dem Meeresspiegel in den bolivianischen Anden gelegene Goldmine. Damit die Kunden auch letzten Endes tatsächlich in den Genuss fair gewonnen Goldes kommen, erfolgen die Schmelzvorgänge streng getrennt in eigenen, vorher gründlich gereinigten Öfen.

Silber
Silber ist seit mehr als 4.500 Jahren bekannt. Vermutlich im 7. Jahrhundert vor Christi Geburt tauchten erste Münzen aus silberhaltigem Material auf. Im alten Griechenland erfreute sich Silber ursprünglich sogar höherer Wertschätzung als Gold. Nach ihm besitzt es die größte Geschmeidigkeit und Dehnbarkeit.
In der Reihenfolge der menschlichen Gebrauchsmetalle rangiert Silber nach Kupfer und Gold an dritter Stelle. Auf unserem Globus kommt das Material zwanzig Mal häufiger vor als Gold. „Sarpu“ nannten es die Assyrer, „silabra“ die Germanen und „argentum" die Römer. Letztere Bezeichnung stammt von dem griechischen Wort „argyros" ab. Und das bedeutet nichts anderes als „weiß-metallisch. Das chemische Kürzel „Ag“ für dieses Metall verwendete Jöns Jakob Berzelius erstmals im Jahr 1814. Für heutzutage recht selten gewordene Uhrengehäuse finden Sterlingsilber 925/1000 (925 Silber- und 75 Kupferteile, Härte 70 Vickers) oder das in Deutschland bekannte 800-er Silber Verwendung. Hier liegt der Kupferanteil bei 200/1000.
Zu den unangenehmen Begleiterscheinungen des Materials gehört schwarzes Anlaufen. Diesen Effekt führen schwefelwasserstoffhaltige Luft oder ausgedehnter Kontakt mit Schwefelverbindungen herbei. Sie reagieren mit Silber zu schwarzem Silbersulfid. Diesem Sachverhalt wirkt die Rhodinierung oder Vergoldung von Uhrenschalen entgegen.
Platin
Platin, ein äußerst seltenes Edelmetall kannte man in Mittelamerika schon vor dem 15. Jahrhundert. Gegen 1750 findet man es auch in der europäischen Literatur. Anfang des 19. Jahrhunderts gelang erstmals die Isolierung der verschiedenen Platinmetalle, darunter auch diejenige reinen Platins, welches eine grauweiße Farbe besitzt und bei ungefähr 1.772 °C schmilzt. Die relative Dichte liegt bei 21,45 Gramm/cm³. Uhrenhersteller verwenden Platin in aller Regel mit einem Reinheitsgehalt von 950/1000. Selbiger, das hohe spezifische Gewicht sowie die schwierige Ver- und Bearbeitung machen Uhren mit zurückhaltend auftretendem Platingehäuse zu einem kostspieligen Vergnügen, jedoch haben Sie stets einen treuen Begleiter. Im Folgenden sehen Sie unsere Platin-Highlights:
Aluminium
In der Erdkruste gehört Aluminium zu den am häufigsten vorkommenden Elementen überhaupt. 1825 gelang dem dänischen Chemiker Hans Christian Ørsted die erste Synthese. Chemisch reines, industriell verwertbares Aluminium ist dem Franzosen
Henri Sainte-Claire Deville zu verdanken. Sein Metall debütierte 1855 während der Pariser Weltausstellung.
Bei Aluminium handelt es sich um ein leichtes Material mit 2,7 Gramm pro Kubikzentimeter Dichte. Durch seine hohe Belastbarkeit eignet es sich beispielsweise zur Herstellung von Flugzeugrümpfen. Uhrengehäuse aus Aluminium, Härte nach Vickers knapp 120, gibt es auch. Aber sie sind relativ selten zu finden. Durch elektrisches Oxidieren (Eloxieren) lässt sich die Oberfläche nahezu beliebig einfärben. Legierung beispielsweise mit Kupfer, Magnesium, Zink, Mangan und Titan steigert die Härte des leicht zu bearbeitenden Werkstoffs.
Bronze
Im Zusammenhang mit Uhrengehäusen ist das archaisch anmutende Metall „en vogue“. So genannte Marine- oder Aluminiumbronze eignet sich besonders gut für Uhrenschalen. Mechanischem Stress, Salzwasser und Korrosion widersteht sie durch einen dünnen äußeren Aluminiumfilm. Nicht zuletzt deshalb vertrauen die petrochemische Industrie und der Schiffsbau auf diesen Werkstoff.
Besitzerinnen und Besitzer einer Bronze-Armbanduhr müssen sich damit vertraut machen, dass die Gehäuseoberfläche im Laufe der Zeit beinahe zwangsläufig Patina ansetzt und sich das Aussehen des persönlichen Zeitmessers allmählich verändert. Positiv betrachtet führt besagter Alterungsprozess zu einer individuellen Note. Körperwärme, Luftfeuchtigkeit, Schweiß und andere klimatische Einflüsse machen Bronzeuhren ergo zu Unikaten.
Stahl
Als einer der beliebtesten und verbreitetsten Werkstoffe für Uhrengehäuse gilt, wie beispielsweise die monatlichen Schweizer Exportstatistiken belegen, edler Stahl. Das Material Stahl
bürgt mit 700 HV für ein vernünftiges Maß an Härte. Das faszinierende „heavy metal“ entsteht mittlerweile in zahlreichen Varianten aus dem chemischen Element Eisen (Fe), mit einer Dichte von 7,86 Gramm pro Kubikzentimeter, einem Schmelzpunkt von 1539 und einem Siedepunkt von 3000 Grad Celsius. Für Uhrengehäuse eignen sich zähe, amagnetische und korrosionsbeständige Edelstahl-Legierungen. Jene mit der Nummer 316 gehört nach 304 zu den am meisten fabrizierten Stählen. In der Industrie besitzt sie also einen hohen Stellenwert. Molybdän verleiht der Legierung 316, bekannt auch als X2CrNiMo18-14-3 eine bessere Korrosionsbeständigkeit. Bei 316 L handelt es sich um eine kohlenstoffarme Variante. Die austenitische Struktur bringt einen hohen Grad an Zähigkeit selbst bei tiefen Temperaturen mit sich.
Rolex verwendet für seine Uhrengehäuse die Legierung 904L oder X1NiCrMoCu 25-20-5. Dieser kohlenstoffarme, höher mit Nickel und Molybdän legierte austenitische Edelstahl bietet im Vergleich mit 316 L unter anderem eine verbesserte Resistenz gegen Korrosion. Maßgeblich hierfür ist auch die Beimischung von etwas Kupfer. Außerdem ist diese Stahlsorte unter allen erdenklichen Bedingungen völlig amagnetisch.
Titan
Mit Titan gelingen zum Beispiel in Luft- und Raumfahrt, Chirurgie sowie Implantologie echte Höchstleistungen. Dass sich das vor rund 200 Jahren entdeckte Metall auch für Uhrenschalen eignet, entdeckten 1980 Ferdinand A. Porsche und IWC. Im Folgejahr gelangte kann der erste Titan-Chronograph auf den Markt. Der Weg vom Hüft- ans Handgelenk macht Sinn. Das Metall vereinigt in sich nämlich alle guten Eigenschaften von Stahl und Aluminium. Sicherheit, Leichtigkeit und Belastbarkeit werden groß geschrieben. Verglichen mit Edelstahl besitzt Titan nur die Hälfte des Gewichts. Seine relative Dichte liegt bei lediglich 4,5 Gramm pro Kubikzentimeter. Andererseits ist es mindestens genauso fest und beinahe hundertprozentig resistent gegen Korrosion. Säuren und Basen können diesem Werkstoff ebenfalls nichts anhaben. Besonders geschätzt werden die antiallergischen Eigenschaften. Positiv ist auch die Unempfindlichkeit gegen Magnetfelder zu bewerten.
Faserverstärkte Kunststoffe
Im zukunftsorientierten Leichtbau gelten faserverstärkte Kunststoffe längst als unverzichtbare Schlüsselmaterialien. Die Merkmale: hohe Belastbarkeit, Schlagfestigkeit, chemisch Stabilität, Gewichtsersparnis und dazu noch Nachhaltigkeit. Kein Wunder, dass die Uhrenindustrie Karbonfasern für sich entdeckt hat.
Zur Herstellung von Gehäusen bietet sich einmal das zuerst von Audemars Piguet praktizierte Schmieden an. Hierfür braucht es exakt geformte Matrizen. In diese Formen legen erfahrene Mitarbeiter ein bis zwei Millimeter dicke Karbonfäden, bestehend aus mehreren tausend Fasern von sieben Mikron Stärke, zusammengehalten von Fäden aus Spezialpolymer. Bei hoher Temperatur von ca. 240 Grad Celsius wird das Ganze mit mehr als 300 Kilogramm Druck pro Quadratzentimeter komprimiert. Der solcherart generierte Gehäusekorpus besteht zu 76 Prozent aus Karbonfaser. Der Rest ist Polyamid.
Hohe Anforderungen stellen die richtige Zusammensetzung, werkstoffadäquate Verarbeitungsmethoden und vor allem die verwendeten Werkzeuge. Von Anbeginn müssen die herzustellenden Teile scharfe Kanten und perfekte Oberflächen. Nachbearbeitung und Politur verbieten sich. Qualität und Optik resultieren also bereits aus der geschickten Anordnung des Rohmaterials in der Matrize.
Hublot, um ein anderes Beispiel zu nennen, nutzt Komponenten aus rund zwei Millimeter dicken, bei der Produktion schon entsprechend vorgeformten Karbonfaser-Platten. Zur Bearbeitung kohlenstofffaserverstärkter Kunststoffe (CFK) in der eigenen Gehäusemanufaktur braucht es kostspielige Hartmetallfräser. Doch selbst die verabschieden sich nach nur zehn Exemplaren. Überdies lässt sich nur etwa 85 Prozent des Ausstoßes tatsächlich für perfekte Uhrenschalen verwenden.
Für die Möglichkeit, den Korpus und andere Gehäuseteile durch viele aufeinander gelegte Karbonfaser-Platten zu produzieren, hat sich Panerai entschieden. Als Ausgangsmaterial dienen Karbonfasermatten. Um jeweils 15 Grad verdreht werden sie aufeinander gestapelt und dann unter Druck bei exakt vorgegebener Temperatur mit Hilfe des gleichen Polymer untrennbar verbunden. Für 18 Millimeter Bauhöhe braucht es insgesamt 126 Schichten. Im gesamten Herstellungsverfahren erweist sich die Fertigung des Rohlings als leichteste Übung. Deutlich anspruchsvoller gestaltet sich das anschließende Fräsen der verschiedenen Karbonbestandteile eines Gehäuses. Glatte und optisch in jeder Hinsicht makellose Oberflächen verlangen viel Knowhow und reichlich Werkzeuge. Schon nach rund zehn Schalen zeigen sich an den Fräsköpfen deutliche Verschleißerscheinungen. Die hohen Preise für Karbongehäuse sind also nicht aus der Luft gegriffen. In dem Bild sehen Sie die Panerai Submersible Quarantaquattro Carbotech Blu Abisso, ein beliebtes Modell mit Carbotech-Gehäuse.
Als Alternative zu Karbonfaser bietet sich Leinen an. Nach dem Brechen der dürren Flachs-Stängel und der Reinigung von Faserresten bleiben Bündel feiner Fäden übrig. Naturleinen entsteht durch das Spinnen auf traditionellen Spinnrädern, anschließendes Haspeln und schließlich kunstvolles Weben. Manuelles Legen unter Beifügung von transparentem Harz führt zu dünnen, aber hoch festen Platten, aus denen Hublot gleichermaßen leichte wie feste Schalenteile herstellt. Die positiven Eigenschaften von naturfaserverstärktem Kunststoff überzeugten die Autoindustrie schon vor Jahren. Immerhin sind derartige Leinenstrukturen dreißig Prozent leichter als Karbon. Aber sie verfügen über fast die gleiche Widerstandsfähigkeit. Im Gegensatz zu schwarzen Karbonfasern bringt beliebig färbbares Leinen Abwechslung ans Handgelenk.
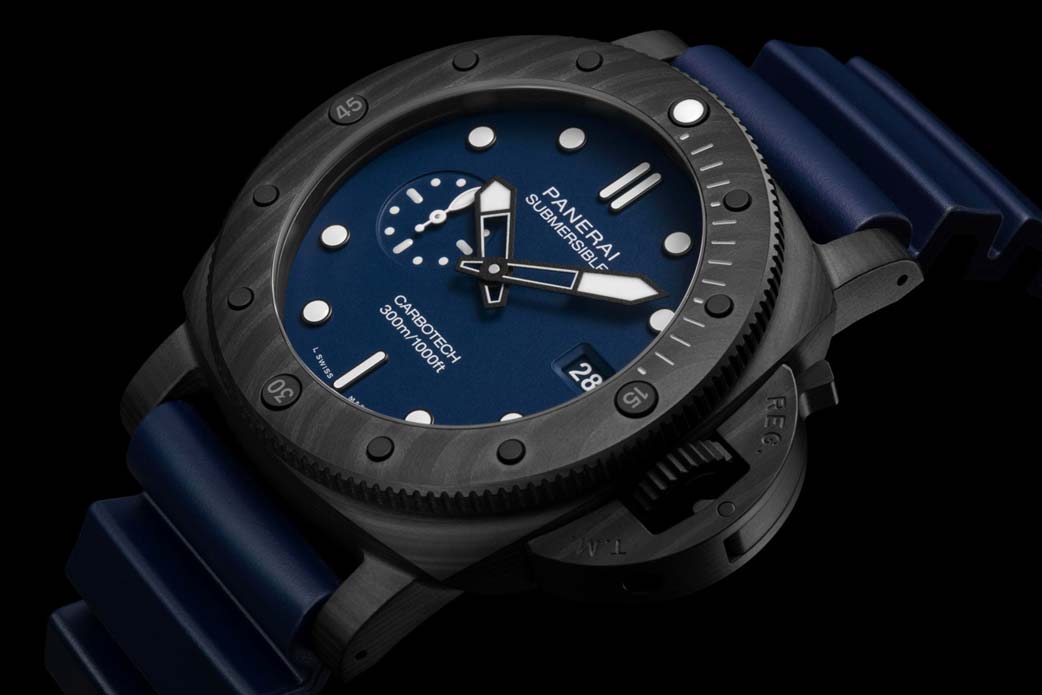
Saphir
Transparente Uhrengehäuse sind nicht grundsätzlich Neues. Das geeignete Material für die Produktion dieser nennt sich: Saphir. Bezeichnetes stellt die Industrie seit ungefähr 1910 in größeren Mengen her. Trotz artifizieller Fertigung entsprechen die chemische Konsistenz und das Eigenschaftenspektrum exakt dem natürlichen Vorbild. Weil Saphir den Korunden zuzuordnen ist, trifft auch die Bezeichnung „weißer Korund“ zu.
Los geht es bei der Produktion mit natürlichem Bauxit, aus dem in mehreren Schritten mikroskopisch kleine Aluminiumoxid-Partikel mit weniger als einem Tausendstelmillimeter Durchmesser entstehen. Im Knallgasofen schmilzt das Pulver durch die Injektion von reinem Sauerstoff und Wasserstoff bei mehr als 2.050 Grad Celsius zu einer zähen Flüssigkeit. Allmählich wächst der solcherart erzeugte synthetische Saphir zu birnenförmiger Gestalt heran. Nach thermischer Stabilisierung steht das Basismaterial für kratzfeste Uhrengläser und seit wenigen Jahren auch extravagante Gehäuse zur Verfügung. Es verfügt über hohe mechanische Festigkeit. Wasser prallt ab, weil der chemisch neutrale Werkstoff keine Porosität besitzt. Indessen erweist sich die enorme Härte von mehr als 2.000 Vickers oder Stufe neun von zehn auf der Mohs'schen Skala bei der anschließenden Weiterverarbeitung als Achillesferse. Weil sich die Teile zunächst einmal völlig matt präsentieren, wird poliert, was das Zeug hält. Diamantbesetzte Schleifscheiben, Diamantpulver und andere chemische Substanzen wie beispielsweise Borkarbid erzeugen Transparenz und perfekte Oberflächen. Weitere Schritte bedingen den Einsatz hoch präziser Laser. Nach dem Assemblieren der Teile zu einem einzigartigen, aber auch kostspieligen Ganzen lässt sich das Uhrwerk in voller Pracht von allen Seiten bewundern.
Zirkonoxidkeramik
Mit Hochtechnologie, Engineering und Rehabilitationsmedizin hat sich dieses Material nahezu unentbehrlich gemacht. Archivstudium fördert ans Tageslicht, dass der deutsche Chemiker Martin Klaproth das Zirkonium schon 1789 entdeckt und im Zuge umfassender Mineralanalysen erforscht hatte. Seine Verarbeitung zu Hochleistungskeramik verlangt nach chemischer Umwandlung durch Brennen. Sauerstoffaufnahme transformiert Zirkonium in Zirkoniumdioxid, dem Ausgangsmaterial für unterschiedliche „Zirkon"-Produkte. Schon gegen Ende des 19. Jahrhunderts begegnet man einer ersten Anwendung in Gestalt des Glühkörpers der 1897 erfundenen Nernstlampe. Danach spürte die Industrie sukzessive das gewaltige Keramik-Potenzial auf. Mitte der 1980-er Jahre lernten erste Uhrenfabrikanten die Vorzüge wie antiallergische Eigenschaften, Leichtigkeit, Kratz- und Verschleißfestigkeit kennen.
Im Herbst 1986 lancierte IWC eine ungewöhnliche „Da Vinci“. Aufwändiger als die Herstellung des keramischen Gehäuserings gestaltete sich bei dieser Armbanduhr das Montieren der verschiedenen „Armaturen“, zu denen auch beweglichen Bandanstöße gehörten.
Bei den Ausgangsprodukten ist zu unterscheiden zwischen Oxiden, also zum Beispiel Aluminium- oder Zirkonoxid, Karbiden, beispielsweise Sililiumkarbid sowie Nitriden wie Silizium- oder Aluminiumnitrid.
Wichtige Kriterien sind in allen Fällen die Reinheit des verwendeten Pulvers sowie die Korngröße im Bereich ungefähr eines Tausendstelmillimeters. Anfänglich erfolgte die Verarbeitung durch Pressverfahren und anschließendes Sintern, sprich Verdichten und Zusammenhaften der winzigen Teile bei hohen Temperaturen jenseits von 1.400 Grad Celsius. Ceramics Injection Molding (CIM) eignet sich zur Fabrikation komplexerer und vor allem präziserer Formen. In diesem Fall wird Keramikpulver zuerst homogenisiert, dann zu Granulat verarbeitet und anschließend mit Hilfe eines Spritzgussverfahrens in Form gebracht. Wegen des auch hier unverzichtbaren Sinterns müssen Fremdstoffe in geringen Quantitäten beigemengt werden. Durch Polieren mit Diamantstaub erhalten fertige Keramikprodukte schließlich ihren seidigen Glanz. Spätestens dann stechen größere Poren oder andere Fehler ins Auge. Solche Gehäuse sind unbrauchbar. Schon bei der Teilekonstruktion gilt es einen entscheidenden Aspekt akribisch zu beachten: das beherrschbare Schrumpfen während des Sinterns. Wer falsch rechnet, erlebt hinterher eine böse Überraschung, weil beispielsweise das Uhrwerk plötzlich nicht mehr in die Schale passt.
Mit einer Härte von rund 1.500 Vickers kann dieser Werkstoff einiges vertragen. Unsanfte Berührung mit scharfen Gegenständen nehmen Keramikkomponenten, darunter mehr und mehr Lünetten auf Stahl-, Titan- und auch Goldgehäusen ebenso gelassen hin wie den schabenden Kontakt mit der Türklinke. Die Kehrseite der Medaille: Keramik ist spröde und mag demnach keine Stürze auf harte Flächen. Im Gegensatz zu duktilen Metallgehäusen, die einen Riss auffangen, zerbricht Keramik ganz einfach in Stücke. In diesem Sinne ist Vorsicht weiterhin die Mutter der Porzellankiste.